The Megawatt Hour periodically highlights energy case studies to expand access to energy efficiency programs and projects. This post and the following one highlight one such case study in which a hotel controls upgrade significantly improves the operation of a four star hotel in Midtown Manhattan. This post provides background on the proposed solution. The second article reviews the impact and payback of the upgrade.
Article by: Tom Leach (Founder, TSI Group LLC)
(201) 704-1149
tom@tsigroupllc.com
An international hotel chain wanted their portfolio hotels to report their environmental status to headquarters as part of their sustainability mission. They didn’t expect that this request would help the hotel achieve the communications goal, save energy, and deliver a 1.2-year return on the investment (ROI).
While the Covid-19 virus affected hotel occupancy after the upgrade was complete, it did not diminish the benefits achieved, nor did it extend the payback period. I’ll address the Covid-19 effects later in the paper. (It wasn’t as big a deal as you might expect. In fact, low occupancy increased the heating the hotel required, which meant the installed controls were even more vital to efficient operation.)
Four-star Hotel in Midtown Manhattan
This hotel was built in 2014, has 270 rooms, and is located in mid-town Manhattan near Times Square. The four-star hotel has a large lobby with a coffee bar and a rooftop bar. The hotel had zero guest complaints regarding the rooms or the common areas during its time in operation.
The hotel’s HVAC system is of high quality, typical of a well-designed commercial building. The HVAC system consists of the following components:
- Four pipe systems for guest rooms and common areas with heating and cooling available 12 months of the year
- 240-ton modular chiller
- Cooling towers
- Condensing boilers
- Duplex pumps for chilled and hot water
- Air Handlers for fresh air makeup
We identified multiple opportunities for improving the energy efficiency of the building.
Construction in NYC is costly: budget overruns are common. In the interest of trying to rein in budgets, buildings undergo “value engineering” or VE. VE leads decision makers to cut the capital budget at the expense of the operating budget. In the era of low-interest rates, this is the wrong tradeoff to make.
Goals of the Controls Upgrade
The management selected this hotel for an upgrade as the energy use for this hotel was much higher than their recently-completed hotel in lower Manhattan. In addition, the company wanted to monitor all hotels remotely and this hotel didn’t have that capability. In addition, management was determined to:
- Maintain guest comfort;
- Reduce energy use to best in class;
- Create a return on investment for the project; and
- Improve hotel monitoring.
Hotel Operation and Controls: The Opportunity
A building is similar to a car in how it consumes energy. The faster you drive, the lower the fuel efficiency will be. With proper controls, building operators can slow HVAC systems and lower energy consumption by adjusting operations to environmental conditions. Most buildings run at full capacity all the time. By adapting a building’s systems to the changing load, the potential for energy savings is enormous.
Here are a few concrete examples:
- Pumps and fans consume power by the cube of their running speed. A pump that runs at 50% speed will consume 87% less energy!
- A boiler will run more efficiently at lower set-points for the supply temperature.
- The chiller and the cooling tower can also work together with the external conditions to minimize total power consumption.
The graph below illustrates how small changes in speed translate to large power savings for pumps and fans. The graph highlights the 87% power savings by reducing a motor speed by 50%. Pump and fan speed are directly controlled by the load in this building.
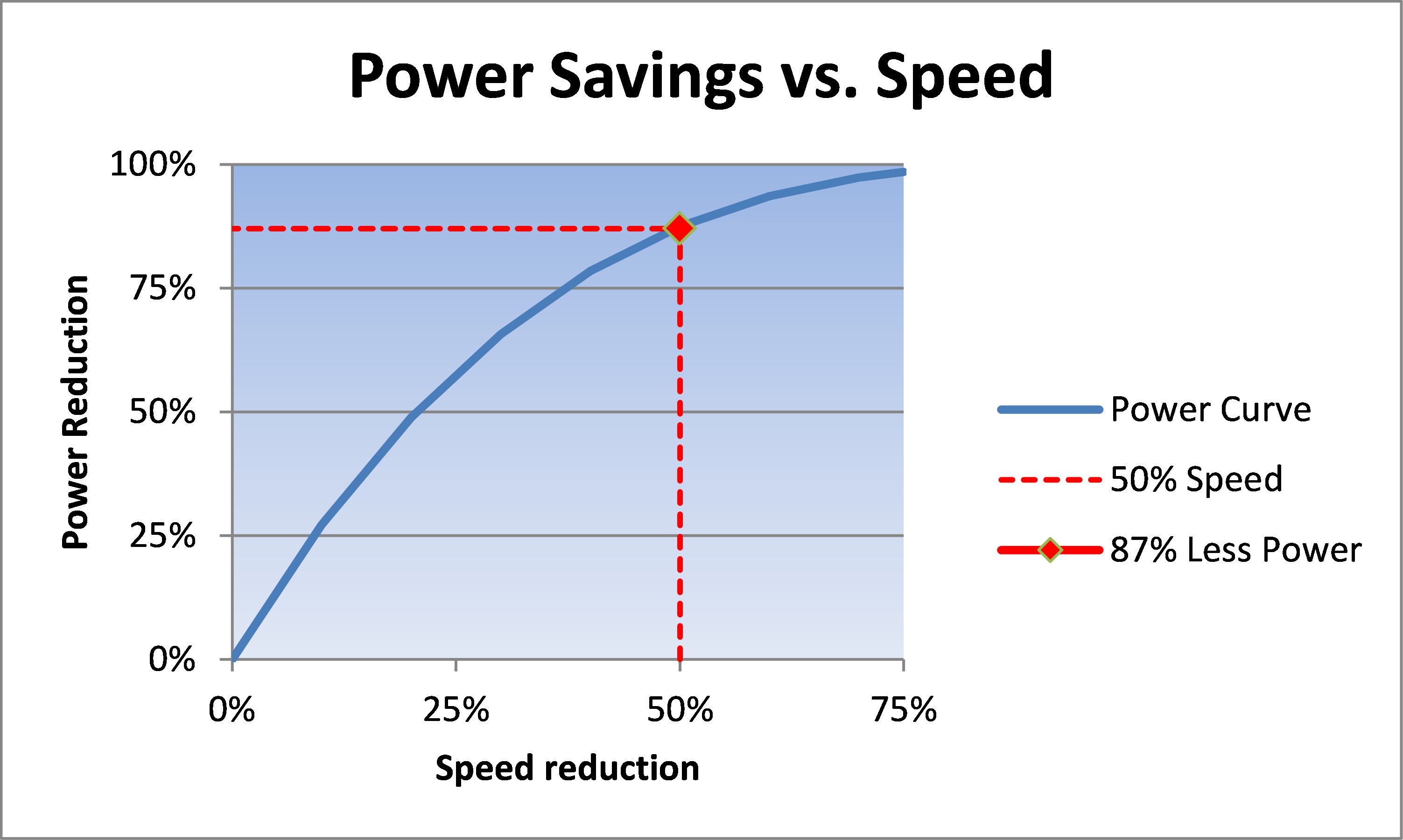
Most buildings run with fixed set-points. As a result, the heating system will satisfy the coldest day in February. Cooling systems will meet demands for the hottest day in August. For pumps, the system sets differential pressure for the worst-case conditions. The chiller, cooling towers, and boilers are all set to handle the worst-case conditions
Case Study: Air Handling Units & Hot Water Pumps
For this hotel, the largest electricity load is the Air Handling Units (AHUs), which provide fresh air for the lobby space. During the winter, the cooling pumps ran too fast because the cooling coil valves were mostly closed. The cooling pump and the valves end up, essentially, fighting each other. The new control system sets the differential pressure based on the equipment’s requirements and the state of demand. By communicating with both the loads and supply elements, the design minimizes energy while satisfying comfort.
The heating system uses the same technique to match the hot water pumps during light loads in the spring, summer, and fall. One of the largest and most important heating loads is guest showers. To make sure guests always have enough hot water, the schedule of expected shower times is programmed into the system to boost both the pressure of the pumps and the boilers’ temperature during periods of high shower demand. (Early morning and early evening.)
Bottom line for energy and financial decision makers: Buildings can be a gold mine for energy savings, if you know where to look.